
CFD DEPARTMENT
JETWINGS TECHNOLOGIES

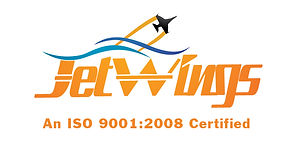
THRUST REVERSAL
Introduction:
THRUST REVERSAL, also called reverse thrust, is the temporary diversion of an aircraft engine's exhaust so that the exhaust produced is directed forward, rather than backwards. This acts against the forward travel of the aircraft, providing deceleration. Thrust reverser systems are featured on many jet aircraft to help slow down just after touch-down, reducing wear on the brakes and enabling shorter landing distances.
The reverse thrust is calculated using the parameters such as mass flow rate, Area of inlet, cascade blade angle and the density. Since the velocity which leaves from the cascade is thrice than the inlet velocity. Form this assumption it can be easily solved using the second fundamental equation of fluid mechanics the Momentum equation.
Since the analysis was carried out in steady state only, the change in properties such as density with respect to time goes to zero. Solving the remaining equation leads to driving boundary conditions. The analysis was carried out using ANSYS CFX Solver manager for nearly 2000 iterations and the residual convergence values are maintained for 1e-05.
Geometry and Mesh:
Fig: Outline image of Thrust reversal cascade configuration 1 ( Reverse Vane).
Fig: Meshing in Reverse Vane cascade thrust reversal.
Analysis:
The analysis carried for different cascade design model and with different velocities. Here the result for 20 m/s velocity conditions result discussed.
Fig: Pressure contour for Reverse vane cascade model.
Fig: Turbulent kinetic energy contour for Reverse vane cascade model.
Fig: Turbulent kinetic energy contour for Reverse vane cascade model.
Conclusion:
From the results and discussion it can be clearly seen that for the low subsonic speed during landing the of around 100 km/hr. (20 m/s) having higher reverse thrust and the reverse thrust has been reduced by reducing the inlet velocity. However the reverse thrust generated is very low for configuration which is having 90 degree cascade blade. The reverse thrust which is generated completely depends on the angle which it leaves at the exit.
The reverse generated with cascade blade for 90 degree turning angle is 0.453720131N for the mass flow rate of 0.0226856kg/s. whereas the reverse thrust generated for cascade blade having large thickness with 30 degree turning angle is 1.628676451N for same mass flow rate. Thus it has increased 72% than the cascade blade angle of 90 degree.
Similarly due to large thickness and other characteristics the thickness has been reduced and the reverse thrust generated is 1.630578337N for same mass flow rate which is around 0.12% increment. Hence it can be concluded that the blade thickness is not affecting the reverse thrust but the blade turning angle does. Again it is also concluded that the turning angle of 30 degree shows better performance than other blade turning angle.
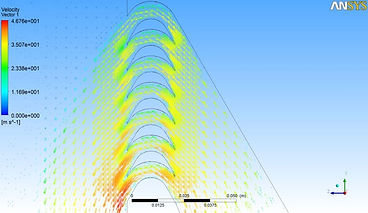



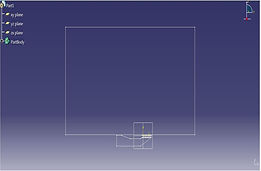